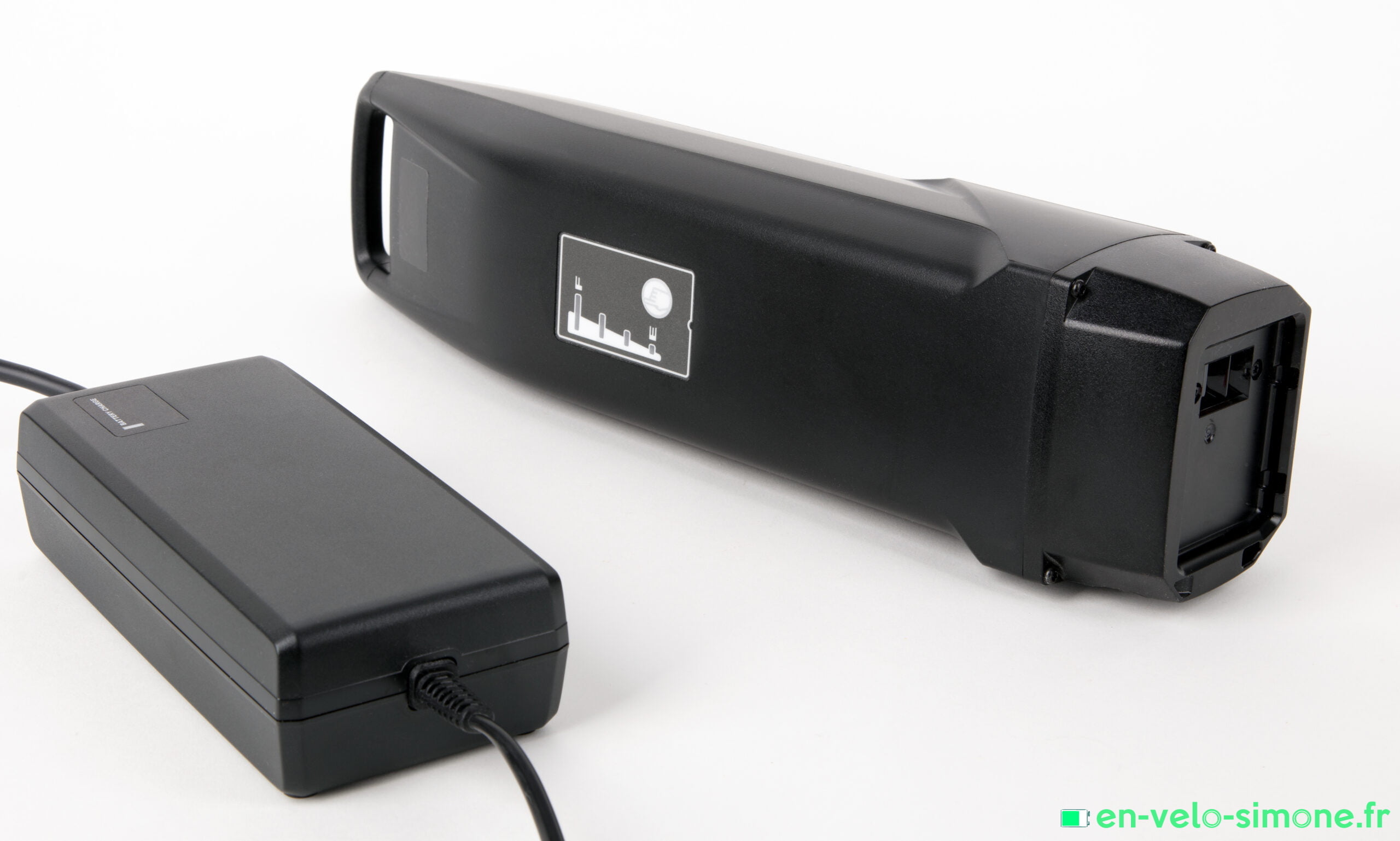
Dans un contexte où la législation européenne intensifie ses exigences en matière de valorisation des batteries, VoltR et Batribox se positionnent en pionniers de la seconde vie des accumulateurs. Leur collaboration, illustrée par l’usine pilote de Verrières-en-Anjou (49), près d’Angers, est une réponse concrète aux défis environnementaux et économiques posés par la gestion des batteries en fin de vie, notamment celles des vélos à assistance électrique (VAE). C’est une histoire qui me touche particulièrement, car elle incarne un espoir concret pour un futur plus durable. Plongeons ensemble dans l’univers de VoltR et Batribox, des pionniers français qui réécrivent les règles du jeu pour nos batteries de vélos électriques, en leur offrant non pas une fin, mais une véritable seconde vie.
Batribox : Un Acteur Historique et Son Évolution
Depuis 1999, Batribox (anciennement Screlec) s’est imposé comme un acteur majeur de la collecte et du recyclage des piles et batteries usagées. L’année dernière, l’éco-organisme a collecté 6 300 tonnes d’accumulateurs via un vaste réseau de 32 222 points de ramassage en France. Batribox innove également avec des initiatives comme la collecte à Lyon par des tricycles à assistance électrique, réduisant ainsi son empreinte carbone.
Face à l’élargissement de la réglementation européenne à toutes les catégories de batteries, Batribox ambitionne d’étendre son activité aux cinq familles d’accumulateurs : appareils portables, moyens de transport légers (trottinettes, vélos, scooters), véhicules électriques, usages industriels, et batteries de démarrage (12 V). Cette diversification stratégique vise à faire de Batribox un acteur central et polyvalent dans la gestion des batteries.
Les Objectifs Européens : Une Feuille de Route Ambitieuse
Je trouve que la législation européenne fixe des objectifs ambitieux pour le recyclage des batteries au lithium : 65 % d’ici fin 2025 et 70 % d’ici 2030. Des taux de valorisation spécifiques s’appliquent également aux matériaux critiques : 50 % pour le lithium fin 2027 (80 % en 2031), et des objectifs encore plus élevés pour le cobalt, le nickel, le cuivre et le plomb (90 % fin 2027, 95 % fin 2031).
Au-delà du recyclage, la réglementation met un accent nouveau sur la seconde vie des batteries. Elle exige qu’un pourcentage minimal d’accumulateurs des moyens de transport légers fasse l’objet de réemploi, réaffectation ou remanufacturage : 2 % pour 2027 et 5 % à horizon 2030. Bien que ces chiffres puissent sembler modestes, Alban Régnier (VoltR) et Emmanuel Toussaint-Dauvergne (Batribox) soulignent l’ampleur de l’organisation et des infrastructures nécessaires pour les atteindre, comme en témoigne leur usine pilote.
Les Scénarios de la Seconde Vie : deux Voies Distinctes
Batribox distingue clairement 2 scénarios pour la seconde vie des batteries :
- Réemploi : Préparer des produits à être réutilisés sans prétraitement majeur (contrôle, nettoyage, réparation mineure). La batterie conserve son usage initial.
- Réaffectation et Remanufacturage : Ces deux processus impliquent un démantèlement de la batterie, une analyse approfondie de chaque cellule, et un tri rigoureux en fonction de leur état.
- Le remanufacturage consiste à reformer une batterie pour la “même finalité ou application que celle pour laquelle elle a été initialement conçue”, avec des contraintes strictes d’homogénéité des cellules (tolérance de 3 %) et une capacité énergétique d’au moins 90 % par rapport à l’origine.
- La réaffectation diffère par un nouvel usage pour les cellules, par exemple des cellules de trottinettes utilisées pour un luminaire. Emmanuel Toussaint-Dauvergne souligne que les cellules peuvent suivre “plusieurs fois les schémas de réemploi, remanufacturage et réaffectation” avant leur recyclage final, maximisant leur durée de vie utile.
VoltR : Un Modèle d’Approvisionnement Stratégique
Pour ses opérations, VoltR s’appuie sur trois catégories de fournisseurs de batteries et cellules :
- Les éco-organismes (dont Batribox) : Ce partenariat a déjà permis d’identifier 85 000 cellules réutilisables sur 8 tonnes collectées depuis 2024, avec une capacité résiduelle moyenne de 94 %. Ces cellules reconditionnées ont une empreinte carbone 86 % moindre que des modèles neufs chinois, générant une économie de 4,5 tonnes de CO2.
- Les recycleurs historiques (ex: Veolia) : Pour ces acteurs, le traitement des batteries lithium est une “charge économique” et un “enjeu de sécurité”. VoltR leur offre une solution en reprenant les cellules exploitables, réduisant ainsi les risques d’incendie liés à l’emballement thermique.
- Les industriels : VoltR signe des contrats d’exclusivité, comme avec Lime pour les batteries de trottinettes électriques, assurant un flux direct et régulier.
Le Processus de Reconditionnement Chez VoltR
L’usine pilote de VoltR combine automatisation et savoir-faire manuel pour le démantèlement et l’évaluation des cellules :
- Démantèlement : Les batteries Lime sont démantelées par une machine laser interne, tandis que d’autres (ex: aspirateurs Rowenta) nécessitent un démantèlement manuel. Les cellules récupérées sont principalement de format cylindrique 18650, qui représente 90 % des batteries en Europe.
- Causes de défaillance : VoltR identifie trois raisons principales de mise hors service des batteries : un BMS de moindre qualité, des soudures défaillantes, ou une cellule dont la capacité résiduelle interne (SoH) est insuffisante, limitant alors l’ensemble du pack.
- Évaluation des cellules : Un “carrousel” développé en interne effectue huit points de contrôle (voltage, résistance interne, aspect extérieur, impédance par spectroscopie). Environ 70 % des cellules sont jugées exploitables et reçoivent un QR Code d’identification pour la traçabilité. Le test ultime est le cyclage (décharge/recharge sur huit heures) pour déterminer la capacité résiduelle précise.
- IA de prédiction : VoltR a développé une IA capable de prédire le comportement futur des cellules. Après des tests accélérés en chambres climatiques, l’IA détermine pour chaque cellule l’usage optimal (ex: 5 ans dans un VAE, 10 ans sur des lampadaires, 6 mois dans une perceuse).
Performance et Clientèle des Batteries Reconditionnées Volt
VoltR équipe déjà des clients prestigieux et engagés dans le développement durable :
- Leroy Merlin pour qui VoltR doit réunir 150 000 cellules.
- La Poste et l’entreprise d’insertion Nouvelle Attitude, qui reconditionne les anciens VAE des facteurs.
VoltR propose des modèles comme les Silverfish (36 V – 16 Ah – 576 Wh) et Hailong (36 V – 15 Ah – 540 Wh), garantis 2 ans ou 500 cycles et identifiés “Made in France”. Leurs batteries reconditionnées sont compatibles avec 50 % des VAE et sont certifiées aux normes européennes de sécurité.
Étonnamment, les clients estiment souvent les batteries VoltR de meilleure qualité que les neuves. Cela s’explique par :
- Un assemblage de packs avec des cellules parfaitement homogènes.
- Des soudures de meilleure qualité (quatre points avec mélange nickel) et un BMS de qualité.
- L’application d’un “escalier de performances” : les cellules sont réaffectées à un usage juste en dessous de leur précédente utilisation. Par exemple, des cellules Lime de 3 Ah (initialement 3,2 Ah) sont utilisées pour des besoins de 2,6 Ah, offrant une autonomie supérieure aux modèles neufs comparables.
Ces batteries sont vendues à un prix similaire aux neuves chinoises (entre 10 % plus cher et 10 % moins cher), mais avec des performances accrues.
Perspectives de Rentabilité et d’Expansion
Les 30 % de cellules non exploitables pour la seconde vie sont renvoyées aux recycleurs classiques, mais sous forme de “black masse” (débarrassée du plastique et de l’électronique), simplifiant ainsi leur travail de recyclage des matériaux.
Le chiffre d’affaires de VoltR est réalisé à 90 % par la revente de cellules et batteries reconditionnées, le reste provenant de la rémunération pour la récupération d’éléments lithium, du nickel et de la valorisation des cartes électroniques. Actuellement non rentable, la société vise la rentabilité sous deux ans, avec une automatisation des process à 90 %.
VoltR ambitionne de donner un “coup de pied dans la fourmilière” et que “l’Europe entière ait une réflexion sur la seconde vie des batteries”. L’entreprise a déjà remis sur le marché 200 000 cellules et espère en livrer 200 millions par an à horizon 2035.
Pour soutenir cette croissance, VoltR, en pleine phase de deuxième levée de fonds, prévoit d’ouvrir en Europe d’ici 2033 :
- Trois usines : La prochaine, de 5 000 m², sera probablement dans les Hauts-de-France.
- Cinq sites de stockage : Un premier s’implante à Durtal (Maine-et-Loire), un ancien silo à grain de 50 tonnes de capacité, avec six mois de travaux prévus.
Les projections de réception d’éléments lithium sont ambitieuses : entre 50 et 100 tonnes en 2026, contre 20 tonnes actuellement, et 2 000 tonnes en 2033. VoltR s’affirme comme un acteur clé de l’économie circulaire, transformant le déchet en ressource et contribuant activement à une gestion plus durable des batteries.

Conclusion
Je pense que l’aventure de VoltR et Batribox, que nous venons d’explorer, n’est pas seulement une prouesse technologique et logistique ; c’est aussi une histoire profondément humaine. C’est l’histoire d’une vision partagée, celle de ne pas jeter ce qui a encore de la valeur, de donner une seconde chance à des milliers de batteries qui auraient fini comme de simples déchets. Derrière chaque cellule reconditionnée, il y a l’ingéniosité d’équipes qui croient en un avenir plus respectueux de notre planète. En redonnant vie aux batteries de nos vélos électriques, trottinettes ou autres appareils, nous ne faisons pas qu’économiser des ressources. Nous contribuons, chacun à notre échelle, à un mouvement plus vaste : celui de l’économie circulaire, où le gaspillage cède la place à la valorisation et à la durabilité. C’est un pas de plus vers un monde où la technologie et l’environnement peuvent coexister harmonieusement, pour le bien des générations futures